Composition of Siemens Frequency Converter and Common Faults and Maintenance MeasuresI. Introduction
Frequency conversion technology is an important development direction of modern power transmission technology. With the development of power electronics technology and power electronics technology, AC frequency conversion technology has gradually matured from theory to practice. Frequency converter not only adjusts smoothly, has wide range, high efficiency, small starting current, stable operation, but also has obvious energy saving effect. Therefore, AC variable frequency speed regulation has gradually replaced the traditional sliding speed regulation, pole-changing speed regulation, DC speed regulation and other speed regulation systems, and is more and more widely used in metallurgy, textile, printing and dyeing, tobacco machine production lines, buildings, water supply and other fields. However, due to the environment, service life and artificial operation and other factors, the service life of the converter is greatly reduced, and various faults occur in use. Next, we will discuss the composition and common faults and Countermeasures of the converter. Generally divided into rectifier circuit, Flat-wave circuit, control circuit, inverter circuit and so on.
251858.jpg
2. Rectifier Circuit
The function of rectifier circuit is to convert AC power into DC power. Rectifier circuit is generally a single rectifier module, but many of the rectifier circuit and inverters are integrated into one module, such as Fuji 7MBI series.
The damage of rectifier module is a common fault of frequency converter. In static state, the damage of rectifier module can be judged by measuring the forward and backward resistance of multimeter. Of course, we can also use voltage meter to test.
Some brands of converter rectifier circuit, the first half of the bridge is controllable silicon, the second half of the bridge is diode. Such as high-power Denver, Delta, etc. A simple way to judge whether thyristor is good or bad is to add a DC voltage (about 10V) to the control pole to see whether it can be turned on in the positive direction. In this way, the quality of thyristor can be roughly judged.
In addition, the rectifier module under 11KW of Fuji converter G9S (P9S) has five functions. Rectifier, pre-charged thyristor, brake tube, power switch tube, thermistor. For example, the name of pin and function of CVM40CD120 rectifier module is for reference.
Rectification: R, S, T, A(+) N-(-)
Charging SCR: A1, P1, G+n (trigger)
Brake tube: DB, N_, G7 (trigger) DB1 B + is its continuous-current diode power supply switch tube: D8, S8, G8
Thermistor: Th1 Th2
G9S (P9S) 15Kw ~ 22Kw, rectifier module for (VM100BB160), its function in addition to rectification, there are pre-charged thyristor. The power above 30 kW is a single rectifier function of rectifier module. More than 75 kW power is a multi-group parallel rectifier module.
3. Flat-wave circuit
Flat-wave circuit contains 6 times frequency pulsating voltage of power supply in the DC voltage of rectifier and rectifier. In addition, the pulsating current generated by the inverter also makes the DC voltage change. In order to suppress the voltage fluctuation, inductance and capacitance are used to absorb the pulsating voltage (current). The DC part of the general frequency converter power supply consists of the main circuit components. Residual, eliminating inductance and adopting simple capacitive filter smoothing circuit.
The capacitance and withstand voltage of the filter capacitor are tested, and we can also observe whether the safety valve on the capacitor bursts. There is no leakage phenomenon to judge whether it is good or bad.
Control Circuit
Modern frequency conversion speed regulation system basically uses 16-bit, 32-bit single-chip computer or DSP as the control core, so as to achieve full digital control.
Frequency converter is a speed regulating device with adjustable output voltage and frequency. The circuit providing control signal is called the main control circuit. The control circuit consists of the following circuits: the "operation circuit" of frequency and voltage, the "voltage and current detection circuit" of the main circuit, and the "speed detection circuit" of the motor. The control signal of the operation circuit is amplified into the "drive circuit" and the "protection circuit" of the inverters and motors. However, when the frequency converter is used in practice, its maintenance is also complicated. This paper provides the following methods to deal with the causes of the fault alarm of the frequency converter control circuit.
Whether the common frequency converter can meet the requirements of the transmission system in use or not, the parameter setting of the frequency converter is particularly important. The incorrect setting will cause the frequency converter to alarm and fail to work properly.
1. Parameter Settings
When the frequency converter is out of the factory, the manufacturer presupposes a value for each parameter. These parameters are called out of the factory (default). The general default value can not meet the requirements of most transmission systems. So before users use the converter correctly, they need to set the parameters of the converter as follows:
(1) Confirm the parameters of the motor and set the power, current, voltage, speed and maximum frequency of the motor. These parameters can be obtained directly from the motor nameplate.
(2) The control mode adopted by the frequency converter is speed control, turn-off control, PID or other ways. After choosing the control mode, static or dynamic identification is usually needed according to the control accuracy.
(3) Set the starting mode of the converter. Generally, when the converter leaves the factory, it is set to start from the panel. Users can choose the starting mode according to the actual situation. It can use panel, external terminal, communication mode and so on.
(4) Given the choice of signal, the frequency of general frequency converter can also be given in many ways. Panel setting, external setting, external voltage or current setting, communication mode setting. Of course, given the frequency conversion can also be the sum of one or more of these ways. After setting the above parameters correctly, the frequency converter can basically work normally. If we want to get better control effect, we can only modify the relevant parameters according to the actual situation. Once the parameter setting applause occurs, the parameters can be modified according to the instructions. If data initialization is not possible, the default values are restored. Then follow these steps to reset for different brands
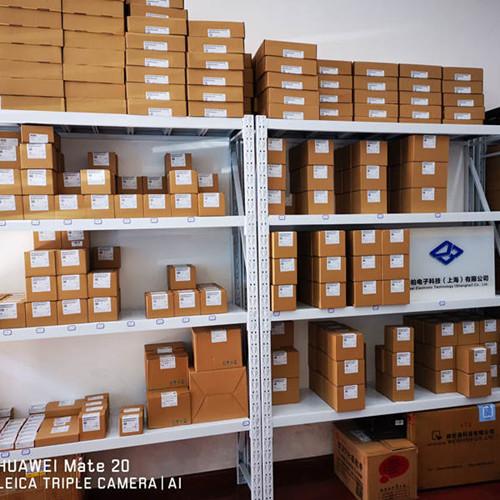